Producción de agua caliente: calderas
Para reducir las emisiones contaminantes y el consumo energético de las calderas de vapor resulta indispensable seguir las siguientes recomendaciones y conocer a detalle su funcionamiento
Leopoldo Guzmán
Los principales problemas que pueden aparecer en el interior de las calderas de vapor están motivados por incrustaciones, corrosiones, arrastres y/o depósitos sólidos. Para luchar contra los inconvenientes antes mencionados, deben acometerse intervenciones en los distintos puntos del proceso:
- Tratamiento físico-químico del agua
- Los diferentes tipos de tratamiento generalmente utilizados, en función de los resultados que se pretenden obtener sobre el agua de una caldera son los siguientes:
- Filtrado de sólidos suspendidos
- Ablandamiento o suavizado para transformar las sales incrustantes en sales no incrustantes
- Desmineralización para reducir el nivel de sólidos totales disueltos
- Deaereación
- Mecánica, térmica y química del agua de alimentación para remover oxígeno disuelto en las calderas y así reducir el potencial corrosivo del agua
- Control de las purgas
- Fondo
- Remoción periódica de los sólidos asentados en el fondo a través de una válvula instalada en la parte inferior de la caldera
- Ventajas de un sistema automático de purga de fondo
- No necesita supervisión del operador
- Minimiza desperdicio de agua tratada y calentada
- Minimiza riesgo de incrustaciones
- Disminuye el envío de agua caliente al drenaje
- Superficie o continua
- Asegurar la calidad del agua dentro de la caldera a través del control continuo de la cantidad de sólidos disueltos en ella
- Ventajas de un sistema automático de purga de superficie o continua
- Mejorar la calidad del vapor generado
- Ahorro del agua tratada químicamente
- Ahorro del combustible para calentamiento
- Menor frecuencia de paros por mantenimiento
- Control continuo del nivel de Sólidos Totales Disueltos
Retorno de condensados
- El retorno de condensados a la caldera tiene los siguientes beneficios:
- Reduce el consumo de agua
- Bajo costo de tratamiento, debido a que el agua es previamente tratada, por lo que presenta un bajo contenido de sólidos disueltos totales
- Ahorro de energía (agua de alimentación a mayor temperatura)
Economizadores
Dada las elevadas temperaturas de humos, se puede lograr una recuperación de calor de los gases de combustión por medio de la circulación del agua de alimentación a la caldera, a través de un economizador ubicado en la chimenea. Dichos gases ceden su calor al agua de alimentación, aumentando así su temperatura. Gracias a esto, el consumo de energía para la producción de vapor disminuye.
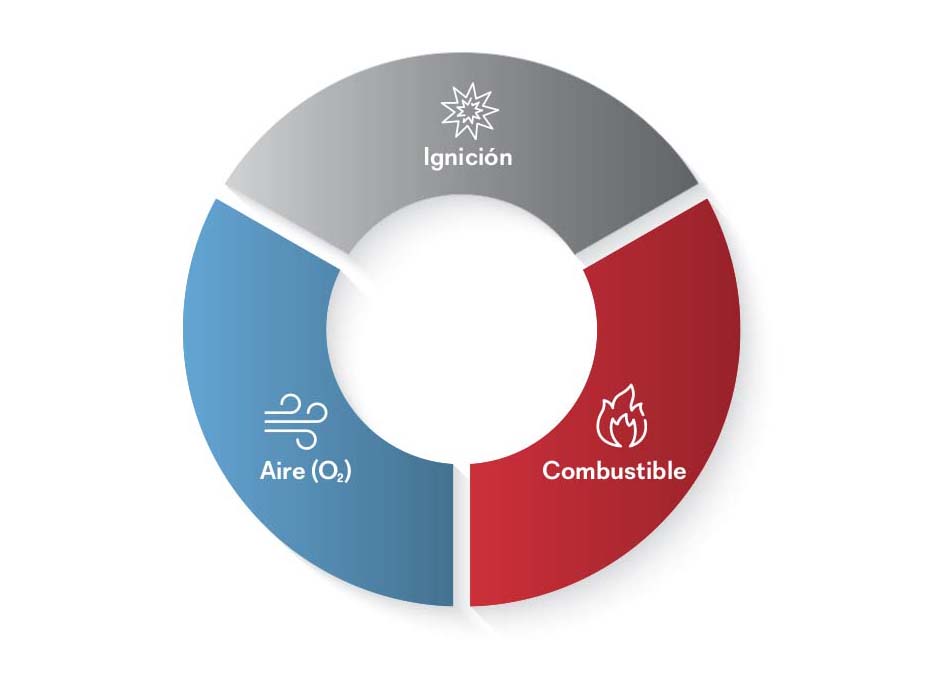
Relación Aire – Combustible Quemador Modulante
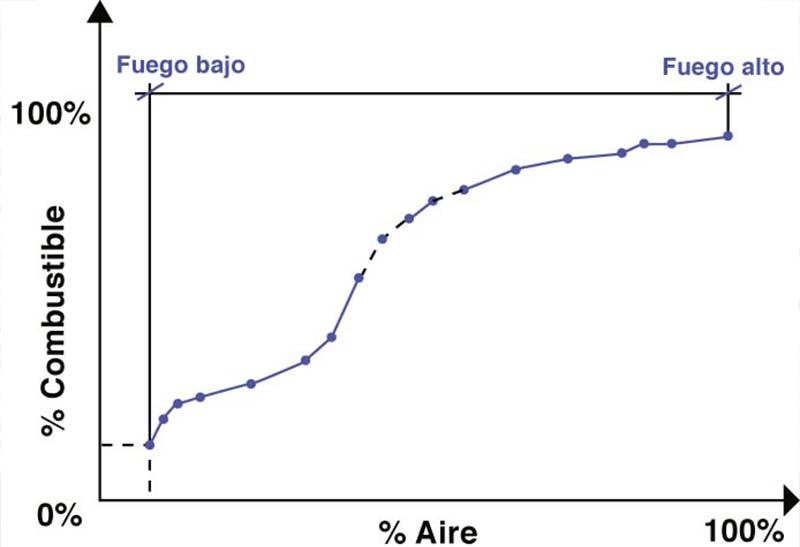
Técnicas de Control
- Actuador Proporcional con Varillaje Mecánico
- Ratio Regulator Relación Proporcional Aire-Gas
- Posicionamiento Paralelo Electrónico
Posicionamiento Paralelo Electrónico
- Control con actuadores independientes para la mezcla aire-combustible
- Permite alcanzar la mejor eficiencia de combustión en todos los puntos de operación del quemador
- Menor producción de hollín, el cual actúa como aislante térmico
- Disminución del punto de bajo fuego
- Ahorro de combustible
Ahorro en el motor del quemador
Adicionalmente, es posible aplicar un Variador de Frecuencia en el motor de Aire de Combustión con los siguientes beneficios:
- Ahorro de Energía Eléctrica
- Regulación de manera precisa del flujo de aire requerido para la combustión
- Reducción del desgaste del motor
Condiciones adicionales de desperdicio de energía
- Distribución de vapor
- Fugas
- Trampas de vapor dañadas
- Inadecuado aislamiento en tuberías, válvulas y depósitos
- Pérdidas de calor en las paredes de la caldera
- Retorno de condensado no recuperado
- Malas prácticas de operación
- Inadecuado diseño o dimensionamiento del proceso
- Mala calibración del quemador y/o sistema de control de combustión
Normatividad aplicable
De acuerdo con el Diario Oficial de la Federación (DOF) la NOM-085-SEMARNAT-2011, Contaminación atmosférica-Niveles máximos permisibles de emisión de los equipos de combustión de calentamiento indirecto y su medición, tiene como objetivo “establecer los niveles máximos permisibles de emisión de humo, partículas, monóxido de carbono (CO), bióxido de azufre (SO2) y óxidos de nitrógeno (NOX) de los equipos de combustión de calentamiento indirecto que utilizan combustibles convencionales o sus mezclas, con el fin de proteger la calidad del aire”. Esta normativa no aplica en equipos con capacidad térmica nominal (generación de calor aprovechable especificada por el fabricante, los manuales de operación y mantenimiento o en una placa adherida al mismo) menor a 530 megajoules por hora (15 CC), equipos domésticos de calefacción y calentamiento de agua, turbinas de gas, equipos auxiliares y equipos de relevo, ni en aquellos que utilicen bioenergéticos.
En el DOF también se señala que esta normativa especifica que los niveles máximos permisibles de las emisiones de los equipos de combustión de calentamiento indirecto, se establecen en función de la capacidad térmica nominal del equipo, del tipo de combustible, de la ubicación de la fuente fija y de las condiciones de referencia, en la Tabla 1 para equipos existentes y en la Tabla 2 para equipos nuevos.
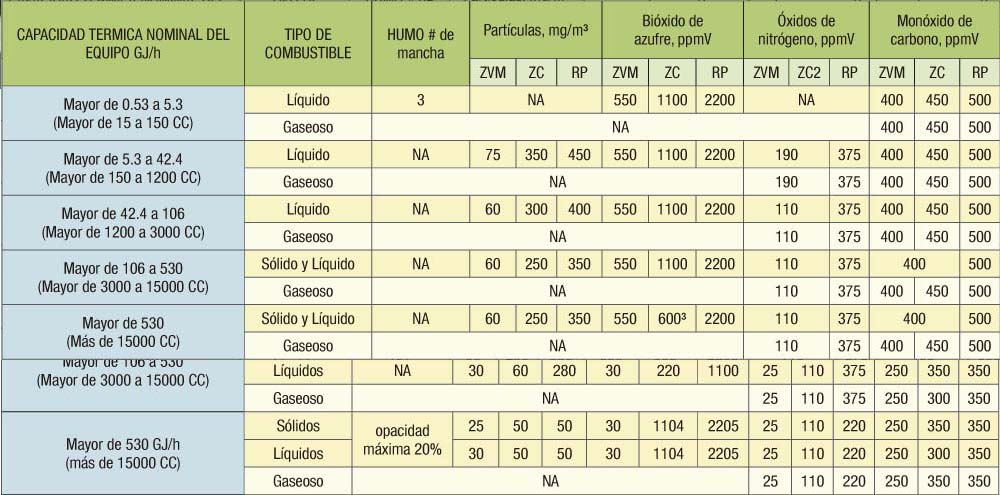
NA: No Aplica
1Para el caso de partículas, SO2, NOX y CO, los límites se establecen como concentraciones en volumen y base seca, en condiciones de referencia de 25°C, 101 325 Pa (1 Atm) y 5% de O2.
Para corregir las concentraciones medidas a la referencia de 5% O2, se utiliza la ecuación siguiente:
Donde:
CR = Concentración calculada al valor de referencia del O2
CM= Concentración medida (Partículas, CO, NOX o SO2)
*OM = Valor medido para el O2 (%)
*OR = Nivel de referencia para el O2 (5%)
*Para valores medidos para el O2 entre 15.1 y 20.9% se utilizará un valor de OM de 15% en esta ecuación de corrección.
2Para NOX, las ZC listadas en los numerales 4.24.4 a 4.24.7, se consideran como Resto del País.
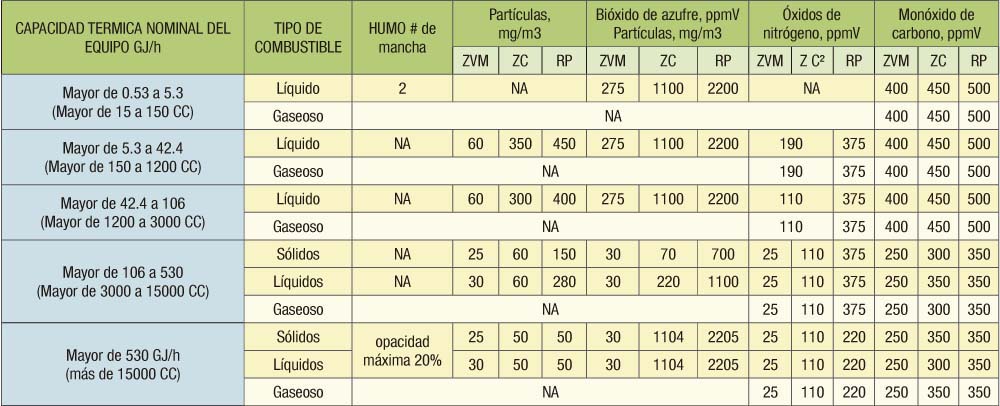
1 Ver nota 1 de la Tabla 1.
2 Para NOX, las ZC listadas en los numerales 4.24.4 a 4.24.7, se consideran como resto del país.
3 Equipos mayores de 1 000 GJ/h; opacidad 20% o menos en el 90% de las horas efectivas de operación.
4 O una reducción del 95% de las emisiones respecto a la emisión potencial máxima de este contaminante.
5 O una reducción del 90% de las emisiones respecto a la emisión potencial máxima de este contaminante.
En caso de cumplir los niveles máximos permisibles de emisión, no se requiere el empleo de equipo de control de emisiones.
Consideraciones para reducción de emisiones
- Control de relación Aire-Combustible (autocarburación)
Consiste en incorporar al sistema de control de relación Aire-Combustible un sensor en la salida de gases de combustión para obtener una retroalimentación de las emisiones en tiempo real. De esa manera, el sistema de control puede realizar ajustes en la curva de combustión de manera automática.
- Selección adecuada de quemador
Éste es uno de los componentes críticos desde el punto de vista de las emisiones contaminantes, la correcta selección de un quemador proporcionará un nivel concreto de emisiones.
Un objetivo es tener una “baja” temperatura de flama, la cual no supere los 1 300 °C que es a partir de ese valor cuando aparecen los NOX.
Curvas de emisiones en Quemadores
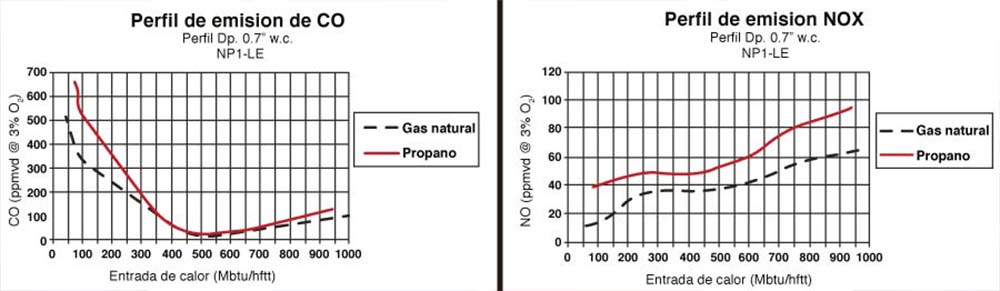
Métodos adicionales de reducción de NOX
- Recirculación externa de humos
- Elementos mecánicos insertados en el hogar
- Tratamiento químico (inyección de amoniaco u otros procedimientos)
Continuidad de operación
- Evitar paros no planeados
- Problemas del proceso
- Fallas de equipos
- Reducción de los tiempos muertos en caso de existir una interrupción no deseada del proceso
- Diagnóstico avanzado de fallas y resolución de problemas
- Estrategias de mantenimiento y de respuesta a fallos
- Análisis e inteligencia de Proceso
- Desempeño de Activos y Equipos
- Prepararse para futuros incidentes que puedan poner en riesgo la operación del proceso
Inteligencia de Proceso de Combustión
- Alarmas y diagnóstico avanzado de fallos
- Mantenimiento predictivo
- Cálculo de eficiencia
- Gestión de KPI’s
- Cadenas de suministro
- Conexión de inteligencia de proceso con KPI’s del negocio
- Envío de Información en tiempo real
- Análisis avanzado para detectar y prevenir problemas junto con datos de proceso
- Monitoreo Local
- Control de seguridad, relación Aire-Combustible y variables adicionales de la caldera
- Instrumentos de Seguridad, Control y Medición de la Caldera
- Caldera
Leopoldo Guzmán
Ingeniero en Electrónica y Comunicaciones, por el Instituto Tecnológico de Estudios Superiores de Monterrey. Cuenta con 13 años de experiencia en sistemas de control de combustión, participando en el desarrollo de automatización y soluciones de ahorro energético para la industria y principales fabricantes de equipo original (OEM) de combustión residencial e industrial en México. Actualmente es gerente de ingeniería y proyectos para Honeywell Thermal Solutions México.